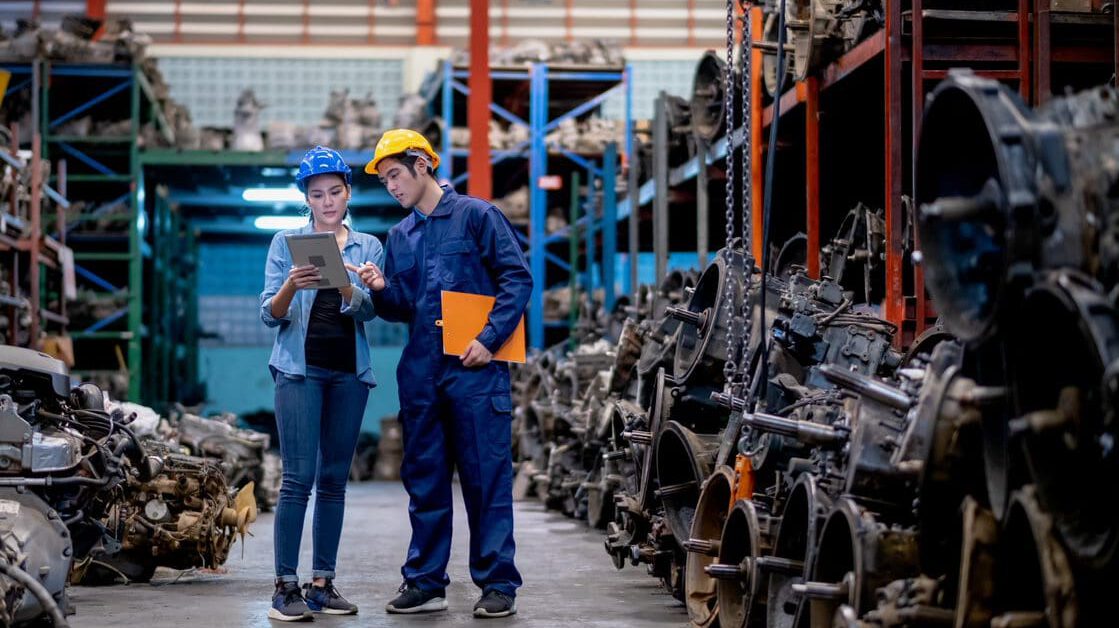
4 Reasons Why Companies Fail at Spare Parts Management (and a Solution to Overcome Them)
We recently attended the Service World Expo Trade Show in Las Vegas, NV. During the event, we spoke to several service providers about issues they are having with spare parts management. For many companies, this function is one of the most challenging parts (no pun intended) of their business.
The typical problems they experience include:
1. Disorganized stock
Spare parts stock found within field stocking locations and individual field service technicians’ vehicles are not well organized or accessible. As a result, technicians may think they do not have a part on hand and place an order for a new one when in fact the part is in their vehicle and just difficult to find.
2. Poor visibility into all stocking locations
Service Management does not have visibility into the volume or value of inventory within their technicians’ trucks or vans. As a result, they make bad decisions about what inventory to purchase, when to purchase it, and where to inventory it.
3. Stock imbalances
Some technicians may be carrying too much stock and/or the wrong stock, while others may be carrying too little. Typically, these stock imbalances can negatively impact a company’s balance sheet and lead to additional costs. For example, unnecessary parts purchases, additional carrying costs, and higher shipping/freight costs.
4. Increased Productivity Challenges
Poor parts management leads to productivity issues and additional costs. If the technician doesn’t have a part on-hand, then they must leave the customer site to pick-up or purchase a new part. It takes longer to complete the service visit leading to fewer service visits per day as well as a repeat/return visit to install the proper part.
These issues occur when companies fail to implement a structured, disciplined, and systemized approach to tracking and managing inventory at the vehicle level. When this happens, parts management becomes a challenge as technicians waste time searching, tracking, and ordering parts that while the company continues to bear additional costs.
Mobile Inventory Tracker applications solve these problems by providing field service technicians with the ability to manage truck stock inventory on any mobile device. By using this type of application, Field Service Technicians can eliminate time-consuming tasks associated with ordering parts by simply scanning a barcode or QR code to check-in or check-out parts from the truck. They can also track parts usage in real-time by integrating with all service transactions including repair orders, parts orders, returns, and warranty claims. Inventory stocking levels can be replenished by automating parts orders based on the stock levels for various parts based on criticality, velocity, and demand characteristics of parts.
Mobile Inventory Tracker applications also provide technicians and service management with real-time visibility to parts availability and location. Through the integration of the mobile app with the back-office system of manufacturers, parts distributors, and channel partners, field service technicians can quickly locate and order parts in real-time. With these connections in place, parts availability can be easily verified, and the right parts can be allocated when dispatching and scheduling service orders for technicians. More importantly, it can help find the needed parts that may be held in the vehicles of nearby service technicians as well as facilitate rapid parts delivery to the job site where the part is needed.
By deploying a mobile inventory tracker application, companies can improve their parts planning to reduce carrying costs, eliminate obsolete inventory, and optimize parts purchasing. In addition, they can increase first-time fix rates by having the right parts at the right place as well as improve technician productivity and utilization by reducing delays and wastes. Furthermore, it can reduce inventory costs and provide actionable insights to optimize spare parts management. In short Mobile Inventory Tracker functionality overcomes the critical challenges that service providers encounter when attempting to ensure that technicians have the right part, at the right place, at the right time.