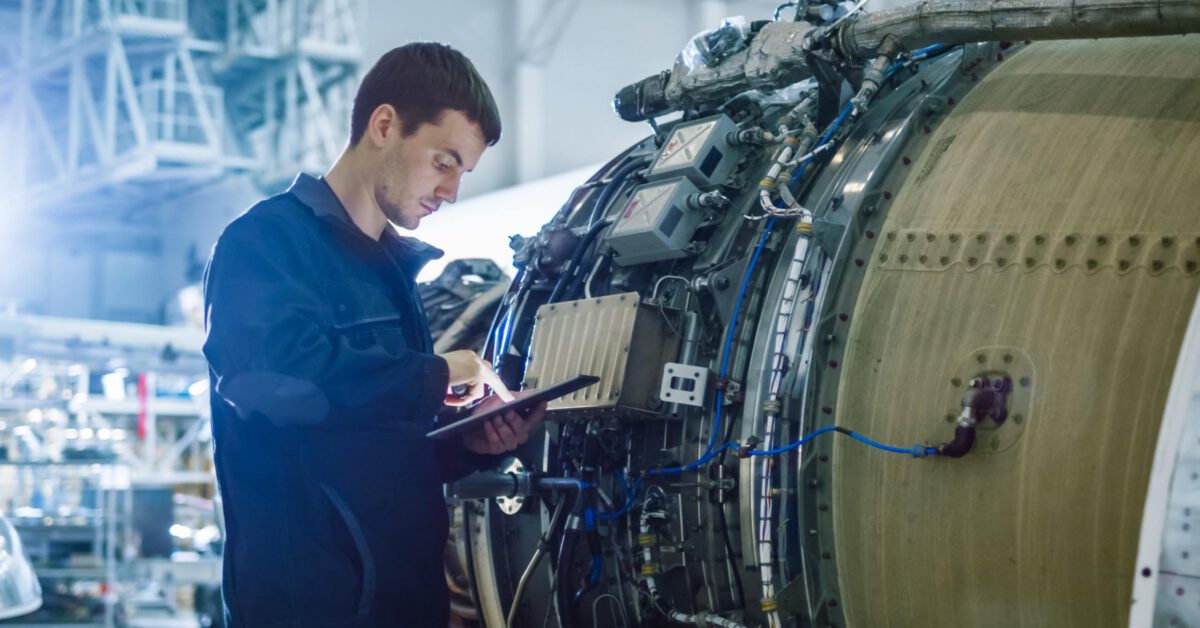
Automated Product Field Inspection Toolbox
Increasing product field inspection obstacles have made challenging and costly activities even more demanding. What was dealing with dissatisfied customers over unexpected product problems is now a communication crisis: field techs struggle without having the tools for quick fixes.
Pile on the pain – inadequate inspections result in increased returns, damaging customer’s perception of brand quality, impacting loyalty, advocacy (the dreaded gripes they spread on their social feeds), and ultimately repeat business opportunities with the product manufacturer and their dealers.
With the ultimate inspection objectives of improved product uptime and customer satisfaction, with maximized operating efficiency in-mind, simplification of achievement becomes the central focus.
Obstacles to simplification exist with multiple inspection process knowledge and reporting systems existing between OEMs and channel partners. It’s even more complicated when manually generated documentation outside of any system is involved. Speed, accuracy, cost-effectiveness (involving warranty management, restocking fees, and refunds), dealer relations, and customer experience all suffer from this environment’s results.
A proven fix: utilizing a single, existing systems-integrated, mobile-enabled platform. It’s a feasible way to add the tools to enable both scheduled and repair/replace inspections, simplifying the flow among everyone involved, unifying procedures, and participants for optimized outcomes, consistently.
Capabilities to look for in inspection management automation starts with actionable inspection history data visibility. This insight enables decreased downtime by proactively detecting issues to keep products operating at peak efficiency while seeing opportunities to improve product quality. Ensuring compliance with regulatory and safety requirements is achievable through an integrated platform’s reporting capabilities.
Mobile access to the platform by service technicians, operators, and customers is another in-field must-have. Either through the web or mobile app (or both), inspections can be performed anywhere online or offline in any language, capturing inspection results and workflow to update customer’s product records.
Maximizing mobile functionality is the game-changer
It facilitates video calls with both those giving or receiving help and start collaboration instantly. Field techs providing remote assistance will have live video streaming ability and can telestrate, freeze images, use hand gestures, and upload photos/videos, syncing with each product’s service records.
Overall, the advantages of this automated product field inspection toolbox include:
- Optimizing product functionality, providing customers peace of mind
- Generating inspection reports and service quote for customers
- Seamlessly notifying dealers of any maintenance or repair needs
- Reducing repair costs by enabling you to detect and fix product problems before breakdowns
- Improving product quality by analyzing inspection results to address the problem’s root causes
- Enhancing Service Plan purchases by including the inspections reports documenting provide proactive service
- Maximizing service and parts sales through eCommerce and authorized dealers.
To see product field inspections in-action, request a demo.