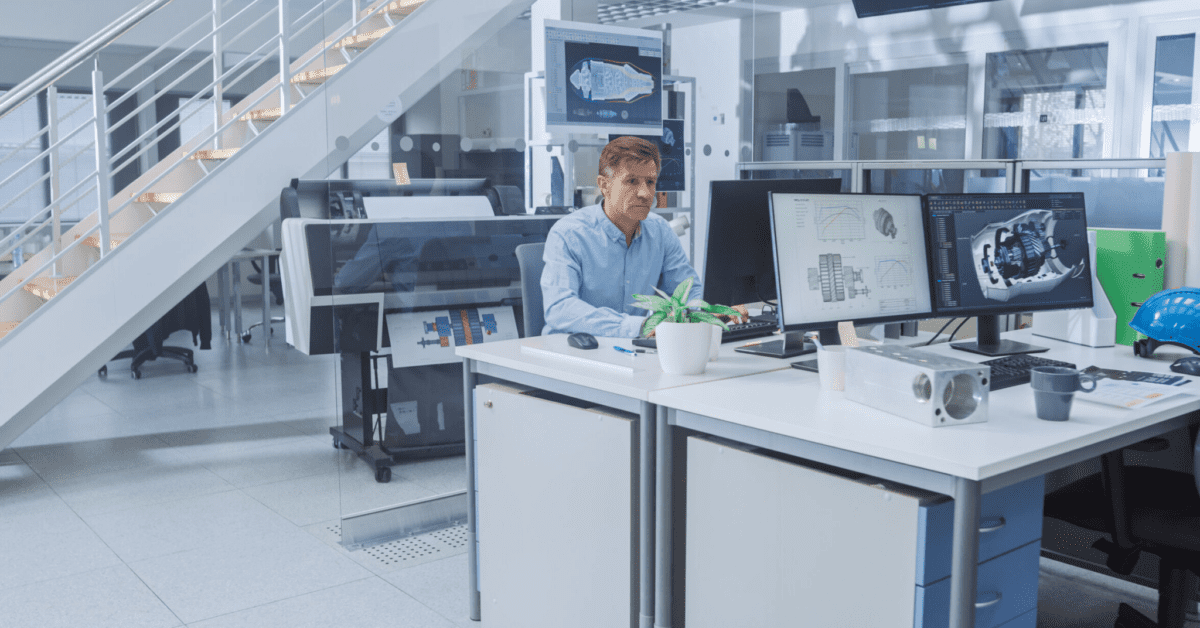
A Warranty Lifecycle Management solution streamlines warranty processes, reduces costs, and boosts customer satisfaction. Yet, many manufacturers use outdated warranty systems that increase costs and inefficiencies. Selecting an efficient solution and dedicated partner is essential.
Why invest in a warranty system?
Manufacturers spend $50 billion annually on warranty claims and make another $50 billion in service contracts. Poor product quality and recalls can hurt brand reputation. Benefits from a warranty system include:
-
- Streamlined processes: Automation can reduce manual processes and costs. Costs can drop from $13/claim to under $1/claim.
- Reduce overpayments: Checking policies and ensuring data accuracy can cut warranty costs 5% to 15%.
- Enhance supplier recovery: Manufacturers can reclaim up to 40% of warranty costs by optimizing supplier processes.
- Product quality improvement: Swiftly addressing quality issues reduces costs and bolsters brand reputation.
- Service contract growth: Using warranty data for service contracts can increase contract revenues and profitability.
With warranty systems, companies can save up to 15% on warranty costs and boost service contract rates by 50%.
Why upgrade now?
In the face of global competition and the rising importance of customer experience, warranties are crucial. Modern warranties can enhance the entire service lifecycle. With the rise of Equipment as a Service (EaaS), integrating robust warranty systems is paramount. Also, automating supplier processes, ensuring compliance, and utilizing customer data for growth are essential. Moving warranty systems to the cloud ensures stability and connectivity.
What’s the warranty system’s role?
When buying a product, it is typically “hired” to fulfill a function, as per the “Jobs-to-be-Done” theory. A warranty system’s role is vast, including tracking assets and entitlements, processing claims, cost recovery, data analysis, and stakeholder access. Many companies have fragmented systems. A holistic Warranty Lifecycle Management system connects all aspects globally.
Choosing the right system
Selecting the correct warranty system is akin to picking the right vehicle for a job. For warranty tasks, a purpose-built system is vital. Often, outsiders underestimate warranty complexities. General-purpose systems might not address intricate warranty needs.
Warranty complexity
While seemingly straightforward, processes like product registration and warranty claims are intricate. They involve validations, entitlement checks, failure coding, and more. Adopting new technologies like AI can also enhance efficiency.
So, while warranties might seem simple, their underlying processes are complex. It’s vital to understand the entire warranty lifecycle and choose a system that addresses all needs comprehensively.
Platform of warranty system
Major enterprise software is grouped into platforms such as customer relationship management (CRM), enterprise resource planning (ERP), and service lifecycle management (SLM). The warranty system, being closely integrated with service work orders, parts, and contracts, aligns most closely with SLM. When deciding on platforms, recognizing this categorization is vital for maximizing benefits from interconnected data.
Warranty costs are influenced by technicians’ decisions on diagnosis and repairs. Easy access to service knowledge can increase a technician’s efficiency and reduce repair costs. The warranty system should be able to draw data from various sources such as ERP, SCM, and PLM to effectively serve different stakeholders.
An integrated SLM platform, inclusive of warranty management, results in better service profitability and consistent revenue from a loyal clientele.
Choosing a team for warranty solution
The success of a warranty system hinges on a knowledgeable team familiar with the manufacturing and warranty sectors. Companies need to hire experienced teams suited to their industry to achieve better outcomes from the warranty system.
True warranty management system costs
While cloud-based warranty software reduces upfront expenses, leaders should consider hidden costs associated with legacy systems. Using cloud platforms for building warranty systems can end in hefty custom developments. Although other enterprise software might offer warranty features, they often don’t cater to the intricacies of the warranty process.
Phased implementation of warranty system
A step-by-step method to implement a global warranty system, considering functionalities or regions, is most effective. The chosen warranty system should be adaptable and consolidated globally for enhanced product and performance insights.
Summary and recommendations
When moving to a new Warranty Lifecycle Management system, select a dedicated solution instead of altering a legacy or existing system. Effective warranty management can result in increased profitability and customer satisfaction. Opt for a trusted partner with the necessary expertise.
Partner for warranty lifecycle management
The Syncron team has extensive experience in implementing warranty systems for global manufacturers. Syncron offers a holistic Warranty and Contracts Management solution that connects all processes and stakeholders. They prioritize manufacturers with a dealer network. To ensure product quality, a seamless customer experience, and reduced warranty costs, reach out to Syncron.