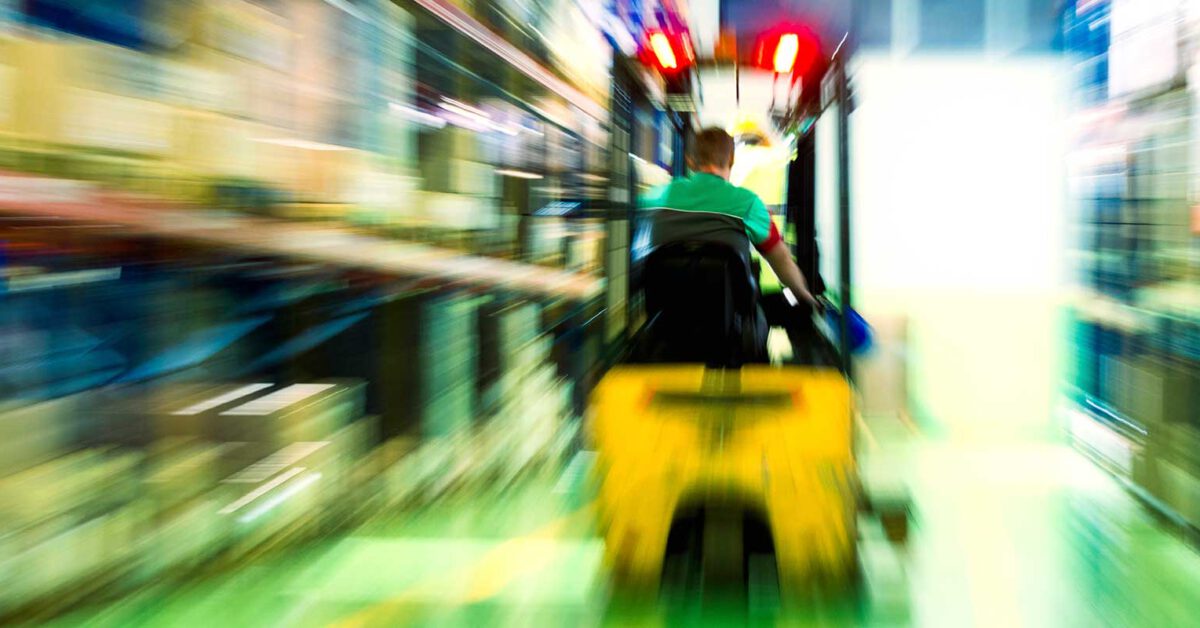
It’s official! Brother Industries, Ltd., a multinational manufacturer of print and imaging equipment, machine tools and industrial and home sewing machines, has joined the Syncron family. By choosing Syncron InventoryTM for its ease-of-use and ROI potential, Brother’s Machinery Business division aims to eliminate manual processes and improve the overall service experience.
Their ultimate goal? To improve product uptime around the world through optimized service parts management.
“At Brother, our focus on service is always top of mind, and we are thrilled to better serve our loyal customers via exceptional service experiences. The Syncron solution will scale with us as we grow, eliminating our current manual processes and ultimately improving customer satisfaction.” – Takashi Yamada, General Manager, Machinery Business Division at Brother
Because of the long lifecycle of industrial equipment (think more than 20 years in some cases) and the variations in downtime severity, manufacturers within the industry need to ensure service parts are available when and where they are most in demand to ensure product uptime. And since industrial machinery is key to manufacturing, as any downtime could bring production lines to a screeching halt, Brother knew they needed to automate their service parts inventory management.
Automation, in this case, helps avoid excess and obsolete inventory – consistently ensuring service parts are immediately available when and where a repair is needed.
Forecasting and planning service parts inventory for products used to be a time-consuming and manual process for Brother. But with Syncron, they’ll be able to eliminate these cumbersome processes, and improve visibility into excess service parts inventory through advanced analytics.
“Today’s most forward-thinking companies realize maximizing product uptime is a key competitive differentiator and revenue-driver. We’re excited to work with Brother to enhance the customer experience through quick and reliable service repairs, as well as improve margins and revenue.” – Johan Stakeberg, Head of Global Sales at Syncron
Brother will initially roll out Syncron among its Machinery Business Division in Japan and China, with the expectation of implementing in more regions, and in other business units in the near future – guaranteeing satisfied customers around the globe.