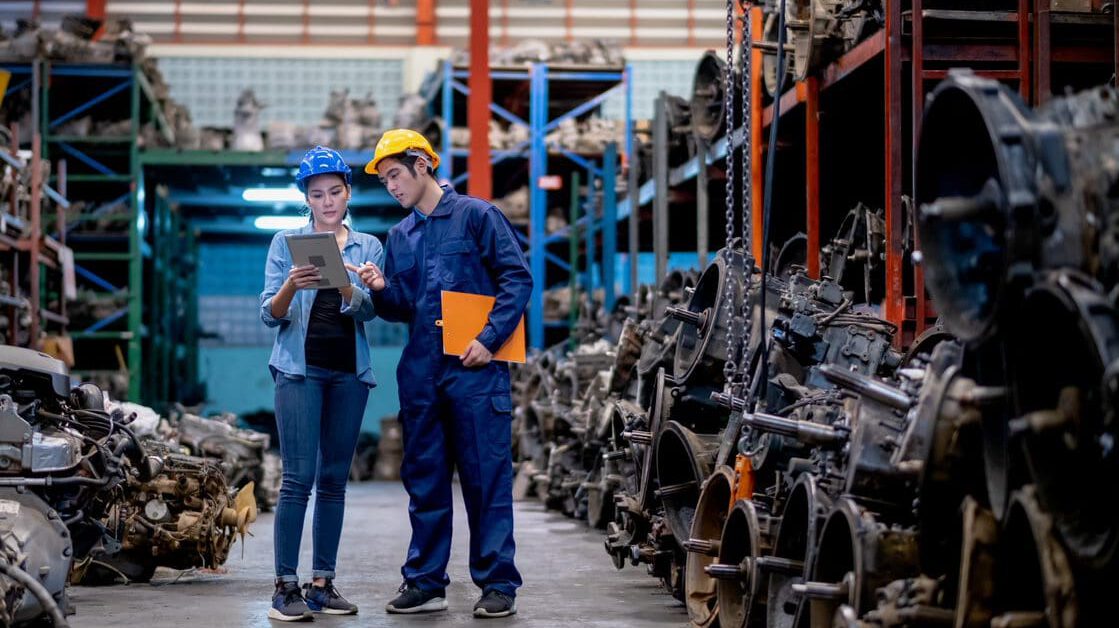
In today’s modern business environment, a nuanced approach is not just a luxury but a requirement, particularly when navigating the intricacies of service parts planning. The business landscape is more or less comprised of two distinct players: steady and predictable production planning and its more volatile counterpart, service supply chain planning. As the complexities of global markets continue to unfold, shifting our focus towards the aftermarket segment isn’t merely a strategy—it’s a paradigm shift promising substantial dividends. Let’s explain why investing in a service supply chain software solution like Syncron is a game-changer.
1. Unveil the complexities of service supply chain planning
Drawing a parallel between production planning and service supply chain planning helps us understand the increasing significance of focusing on the aftermarket. While production planning moves at a predictable pace, the service supply chain dances to a different, more volatile tune. It contends with global supply chains and fluctuating seasonal demands. In the context of aftermarket planning, the stakes are high, the networks vast, and the demand patterns often sporadic, warranting a resilient solution amidst these challenges. This is where Syncron shines, adeptly managing high-value assets across diverse sectors and ensuring streamlined operations even when faced with the complex web of international markets and demands.
2. Shave down inventory costs: Combat the high cost of capital
The pressures of escalating inventory costs and time-sensitive repairs often create a backdrop of intense operational pressures on OEMs and their networks. Syncron steps into this high-stakes environment as a catalyst for change, enhancing part availability between 12 – 17.5% while curbing inventory costs by 15%.
Syncron’s approach, 100% centered on the aftermarket, differs from traditional supply chain software capabilities, effortlessly navigating through erratic demand patterns and the looming obsolescence complexity. It’s more than a strategy; it’s a roadmap to fiscal prudence, guiding businesses to optimize and foster sustainable growth.
3. Increase customer satisfaction: The gateway to brand loyalty
A satisfied customer transcends being a mere statistic; they embody the potential for sustained business and brand loyalty. In an environment where competition is fierce and constantly evolving, a stockout isn’t a simple roadblock—it’s a potential chink in the armor of brand reputation. Syncron rises to this challenge, minimizing stockouts and nurturing a reputation that resonates with reliability and superior service quality. By facilitating experiences that foster brand loyalty, businesses can cultivate a customer base that not only returns but advocates for your brand.
4. Up the uptime: The nexus of efficiency and productivity
Uptime is more than a metric; it’s a testament to a business’s efficiency and productivity. Syncron champions the cause of maximizing uptime, orchestrating a seamless operational flow that fuels business growth. By focusing on keeping equipment running smoothly, Syncron doesn’t just mitigate downtime but paves the way for enhanced productivity, transforming potential losses into profitable uptime. In a landscape marked by volatility, particularly with pricing oscillations stemming from disrupted supply chains and soaring interest rates, Syncron stands as a beacon of stability, fostering business resilience and adaptability.
5. Boost efficiency and visibility: Your vantage point in business
With agility being a top priority for service organizations, Syncron extends beyond offering a solution—it provides a vantage point, a panoramic view of the evolving business landscape. Through automation, teams can prioritize critical areas, while real-time visibility into inventory levels guides business-transforming decisions. It’s about crafting a narrative of success, fueled by data-driven insights and a pulse on market trends, shaping a future where your business doesn’t just keep up but leads.
Craft a future of resilience and growth
As we navigate a business environment marked by unprecedented shifts, the reevaluation of service supply chain strategies transforms from an option to a necessity. It’s about securing your foothold in the market, nurturing a growing customer base, and crafting a brand narrative that resonates with excellence and reliability.
In this transformative journey, we invite you to converse with a Syncron professional, your guide in this rapidly evolving landscape. This conversation could mark the genesis of a trajectory characterized by sustained growth and enhanced customer satisfaction, steering your business toward a future where potential meets unparalleled growth