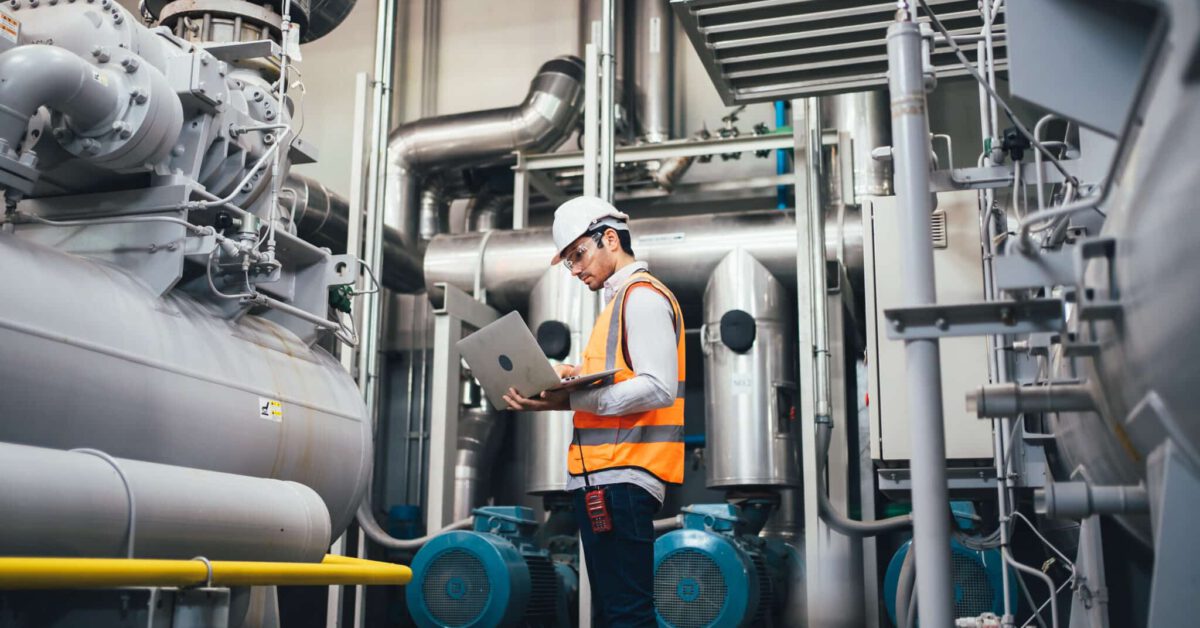
The labor market has been turned upside down by macroeconomic factors like the COVID-19 pandemic and its aftermath, supply chain disruptions and the Great Resignation, where skilled workers are leaving their jobs and creating significant gaps in the workforce. This trend is prevalent across many industries, including industrial engineering (IE), which is seeing a wave of engineers, technicians and tradespeople retire, take valuable knowledge with them and leave behind skills gaps that need addressing.
Additionally, technological advancements in manufacturing have created another gap. Existing workers may lack the expertise to operate and program newly adopted platforms, and the employees who possess such skills are in short supply and in high demand. To mitigate these challenges and ensure success, manufacturers must optimize their service offerings through technician enablement.
Closing the skills gap with data analysis and automation
One approach to addressing IE skills gaps is through harnessing advanced data and analyzing intelligent insights. The digitization of the manufacturing industry has created a wealth of information generated by machines and processes. By examining this data, service leaders can easily identify skills gaps and develop targeted solutions, recommendations and training programs. By analyzing such insights into skills deficiencies, service organizations can implement strategies that strengthen their capabilities and bridge the gap between existing skills and emerging technology.
Automation is another powerful tool for technician enablement and service optimization. Automation can be embedded in machines or integrated into processes, reducing dependency on specific engineering and maintenance skills.
For example, automated maintenance processes can troubleshoot issues and proactively address potential problems before they occur, reducing the reliance on specialized skills for day-to-day operations. Automation increases operational resilience while also freeing up skilled workers to focus on more complex tasks, resulting in maximized productivity, increased efficiency and a superior customer experience.
Investing in people, not just tech
Service optimization and technician enablement shouldn’t focus solely on the technology or platform supporting these processes—investing in people is equally important. Service organizations should make training opportunities readily available to their employees, which can simultaneously offer current employees the opportunity to upskill, expand their capabilities and provide a solid foundation for new hires. Training programs can cover a wide range of topics, from technical skills to machines and software, as well as “soft” skills like leadership, problem-solving and communication.
By investing in people and offering opportunities for ongoing professional development and continuous growth, service organizations can create a skilled, agile workforce capable of adapting to changing technologies and market demands, resulting in higher employee retention and satisfaction and a superior customer experience.
Streamlining processes for operational efficiency
A connected service ecosystem is fundamental to service optimization and technician enablement. Implementing an intelligent, comprehensive system that transforms and connects your aftermarket service lifecycle with streamlined planning, intelligent pricing and exceptional service can streamline processes, provide greater visibility and maximize operational efficiency.
A connected ecosystem doesn’t only benefit your bottom line—it creates a better experience for field teams, making everyday work easier, faster and more transparent. A connected service platform can also facilitate knowledge transfer and collaboration among team members, empowering them to learn from each other and take advantage of their collective expertise. This practice helps businesses retain skills even if employees leave the organization, ensuring that critical information is preserved within the knowledge base and not lost due to employee turnover.
Service optimization through technician enablement is essential for businesses in the manufacturing industry to thrive in today’s competitive landscape. By taking advantage of advanced data, connected processes and automation, service organizations can bridge skills gaps, maximize operational efficiency and become more resilient. Investing in people and providing training opportunities help foster a skilled workforce capable of adapting to evolving technologies, economic uncertainty and fluctuating market demands.
Paving the way for a skilled workforce
Implementing a connected service ecosystem creates streamlined processes and maximizes visibility, leading to better team experiences and retention. By prioritizing service optimization and technician enablement, service organizations can become more employee-focused, operate more efficiently and deliver higher-quality products and services to their customers.
Embracing technician enablement empowers the next generation of industrial engineers to tackle challenges, unlock new opportunities and drive innovation in the manufacturing industry. It’s time to pave the way for a skilled, agile workforce that can thrive in today’s dynamic landscape.