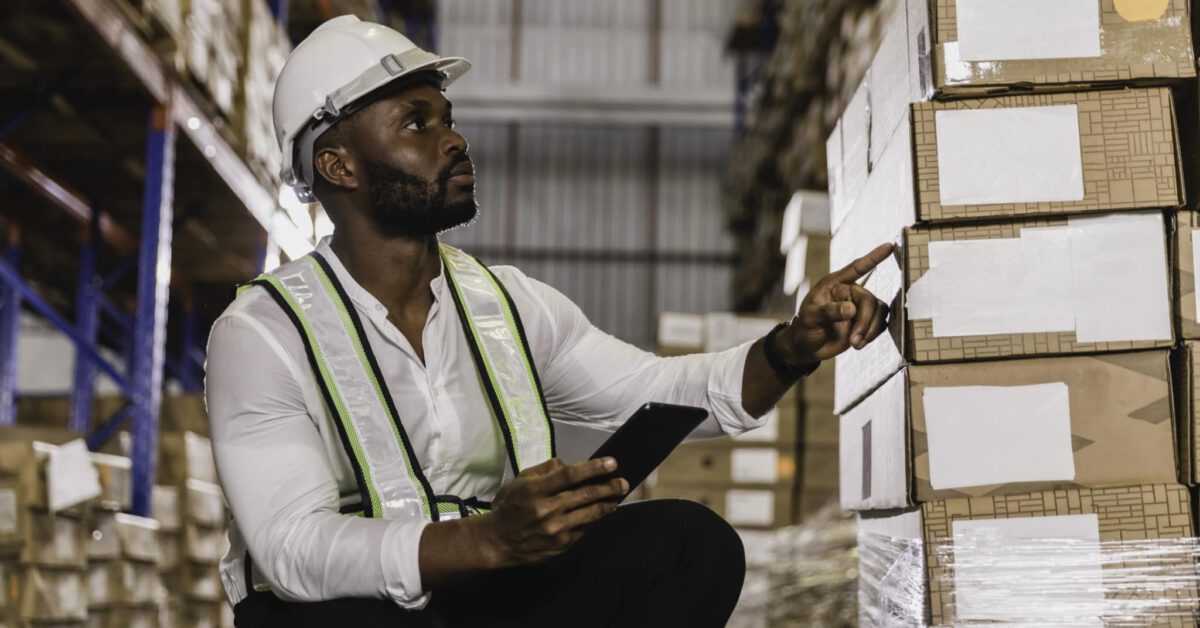
Why Inventory Planning Requires Much More Than a Good Forecast
Do you find forecasting difficult in your aftermarket business? Can you still maintain a 95%+ fill rate even with lower-than-expected forecast accuracy? The answer is YES! Just like a football team requires strong coordination between the halfback, center, and striker…..a good inventory plan requires much more than a good forecast.
In fact, most people don’t realize that fill rate settings, optimal order quantities, and planned lead times are the biggest part availability drivers in the aftermarket. But that’s not the only thing that makes aftermarket forecast very challenging. Usually, around 10-15% of the portfolio are predictable and can be managed with simple techniques. The remaining 85-90% has intermittent, erratic and lumpy demand patterns, and require a different approach. In particular, spare parts with lumpy demand, where the demand history contains a large percentage of zero values alternating with random peaks of non-zero demand, pose problems. For such items, there are no patterns or structures in historical demand, and there are no statistical methods that can provide a good result.
Better forecasting
For better forecasting in the aftermarket, additional tools must be used, such as machine learning, installed base forecasts, connected inventory, new machine sales, and various causal factors. Having the latest technology allows a manufacturer to apply these advanced techniques and help create the best possible forecast. Statistical forecasting can be tailored to the aftermarket: Based on the frequency and variance of demand, statistical methods are applied that fit best. In addition, the causal forecast takes into account all available information on the installed base, the use of spare parts and the sale of new equipment. For the final forecast, statistical and causal forecasts are mixed to achieve the best result.
But even the best possible forecast does not make customers happy. Customer satisfaction comes from good service and parts availability, which means inventory optimization comes first. The standard deviation of the forecast is more important than the demand forecast itself. The forecast is only one input for the correct calculation of safety stock, reorder level and optimal order quantities, which enable delivery orders to be placed for the right items at the right time.
Maximize parts availability
Due to the large differences in the criticality of spare parts, there are different requirements for the service level and thus for the safety stock. For spare parts that are considered very critical or have a long lead time, the safety stock should be large. However, for very critical items with day-to-day delivery lead time, safety stock may be very low or not required at all. To maximize parts availability and thus customer satisfaction, it is necessary to optimize the targeted service level at the parts level.
Optimize your aftermarket performance
Why should spare parts planning be limited to forecasts when there are deeper ways to optimize inventory? Based on customer experience, the true value comes from optimizing inventory and targeted service levels, resulting in reduced inventory, improved service levels, lower shipping costs, improved customer satisfaction and loyalty. Optimizing your aftermarket performance means more than just optimizing individual service processes. True optimization addresses the synergies between all processes in the entire aftermarket service chain, from start to finish.
Did you know that Syncron is the only aftermarket provider that can offer a holistic solution that goes beyond inventory planning and covers the entire service supply chain? For more information, click here.