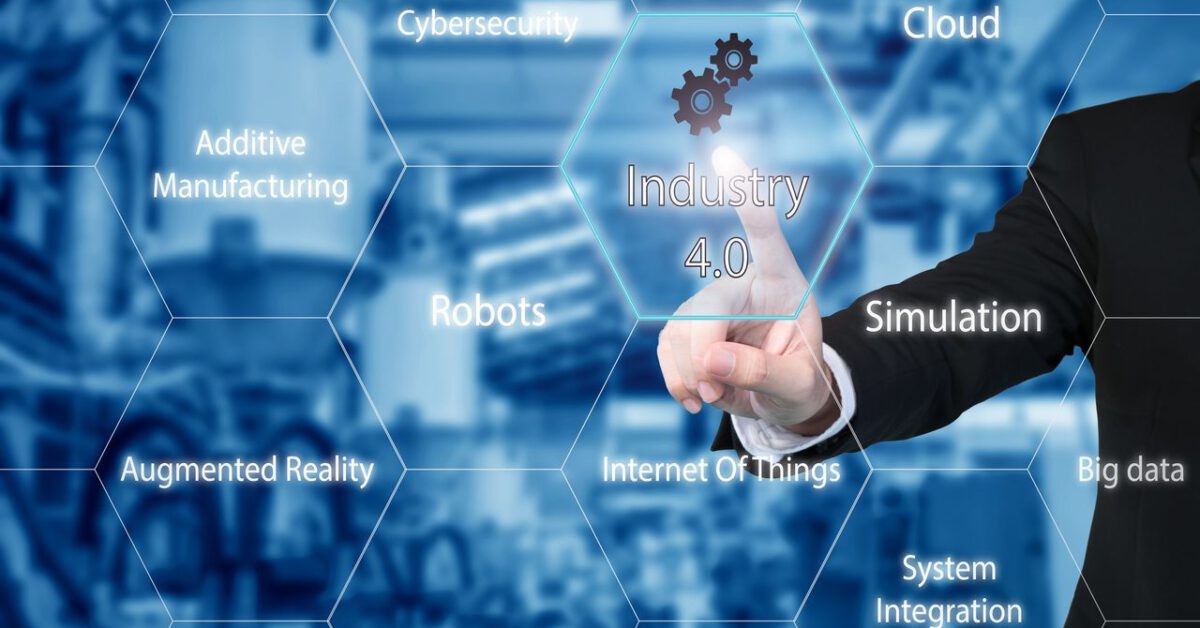
パンデミック後の需要の拡大が製造業に与える影響
筆者:シンクロン プロダクトマネージャー ステファン・シアンダー(Staffan Theander)
パンデミック関連の規制が解除されてサプライチェーンが加速。今後の需要急増に対応するために製造業者は計画策定を開始すべき。
世界の製造業者にとって、この1年は厳しいと言わざるを得ない状況でした。主要産業や日常生活が停止すると同時に、設備や自動車が休止し、多くの場合は使用も整備もされない状態でした。売上が激減し、あらゆる製造業者とサプライチェーンがそのあおりを受けました。しかし、予防接種が普及して規制が緩和されたことで、通常の生活に戻りつつあります。材料と熟練技術者の両方の調達が容易になれば、サプライチェーンが加速します。今後は需要の急増が予想されるため、製造業は顧客のニーズに応えられるように計画を立てておく必要があります。
ブルウィップ効果からの回復
売上が大幅に減少した場合は、予測を調整した上で注文レベルを調整することが必然の対応であり、これは多くの場合、自然発生的に行われます。売上の減少に伴う資金繰りの悪化により、在庫削減への圧力がさらに強まります。消費量が減少し、再発注点が減少することで、サプライチェーンの各上流層の変化がさらに大きくなります。多くの場合、このようなサプライチェーン全体への伝播と増幅は「ブルウィップ効果」と呼ばれます。これは2008年の金融危機の後に見られた現象と同じです。
例えば小売需要が25%減少した場合は、小売業者が既存の在庫を使い切ってしまうため、製造業者の受注量がさらに減少する可能性があります。その結果、製造業者の需要が50%減少し、製造業者はティア1サプライヤーへの発注を減らし、ティア2サプライヤーはティア1サプライヤーへの発注をやめる、というように連鎖していくことになります。
流れが変わり、世界経済が再び動き出した今、ほぼすべての地域で需要が高まっています。小売業者と製造業者が対応する際には、消費量の増加をはるかに上回る量の発注を行うと同時に、緩衝在庫の再構築も必要となります。そしてこの影響は再びサプライチェーン全体に波及します。
需要増、生産力減
事情はさらに複雑で、多くのサプライヤーが景気後退に対応してすでに生産能力を削減しています。また、規制上の理由で廃業したサプライヤーや、部品や製品の供給ができなくなったサプライヤーもいます。その結果、増加する需要に対してサプライチェーン全体の生産能力が低下します。では、製造業者はどう対応すればよいのでしょうか。
純粋なフルシステムを運用している場合は、仕掛品やサプライチェーン上のユニット数に上限を設けることで、サプライヤーからの注文を待っている未処理の注文が大量に滞留してしまうことを防げます。また、真の需要ではなく、誤ったシグナルに基づいて予測量を増やすと、過剰な在庫を抱えることになるので注意が必要です。そうなると、今度は消費量を下回る水準まで注文レベルを引き下げることになり、そのサイクルが繰り返されます。
各レベルの需要に基づいて予測することは、一見すると適切な計画策定方法のように思えますが、実はこれは製造業者とサプライヤーにとって長期的には適切な方法とは言えません。不確実性の高い時期や消費者の需要が落ち込んでいる時には、事業規模の即時適正化が正当化されます。過剰反応する傾向が問題なのです。
見える化で効率アップ
注文過剰・不足間での変動を避けるためには、実際の消費量を可視化する必要があります。これは需要パターンの変動時には特に重要になります。また、予測や計画に販売時点や消費者のデータを含めることも重要です。サプライチェーンを端から端まで綿密に計画できれば、問題を軽減できる可能性が高まります。そのためには、末端市場をより深く理解し、サプライヤーと知識を共有する必要があります。両者が結局は顧客の要求にできるだけ効率的に応えたいと考えているのです。
サプライチェーン管理のポイント
運用面において、顧客へのサービス提供とサプライチェーン問題の克服の鍵となるのは、在庫を縦横に再分配するための効率的なITサポート付きネットワークです。独立した小売業者や販売業者がビジネスモデルに含まれている場合、販売業者が直接的に競合していても、販売業者間の輸送を実現して奨励すべきです。これにより、エンドユーザー体験を向上させることができ、さらには、自社の配送センターへの緊急の取り寄せ注文が発生しても迅速に回復できると同時に、ネットワーク内の過剰在庫をバランスよく解消できます。
組織は実績のある戦略や手法を導入することで、パンデミック後の波に乗り、顧客サービス能力に及ぶ無知効果の影響を最小限に抑えることができます。次のような点に注目してみてください。
戦略的なサプライヤー管理
ビジネスの重要度と途絶発生度に基づいて部品とサプライヤーをセグメント化すれば、調達戦略をサプライヤーごとに差別化できます。
リードタイム管理
多くのサプライヤーにおいて、一時解雇、生産能力の低下、規制上の理由などにより、リードタイムが長くなります。システムやプランニングのリードタイムを手動で調整することで、今すぐ先手を打つべきです。通常の状態に戻ったときには、ダイナミックなリードタイム調整で有利な立場を維持できます。
在庫配分
重要部品の在庫が少ない時に、サプライヤーが休業した場合や、特定の場所で重要部品の供給が制限された場合、その重要部品の在庫の割り当てには在庫配分が役立ちます。注文明細行に優先順位をつけ、緊急性に応じて少量を配分します。
外れ値管理
在庫レベルを過剰に修正して不適正な在庫レベルを目標にしてしまうことがないように、需要の急上昇や急下降に注意し、これらのレベルを予測データから除外します。
プル/消費ベースの在庫最適化
再注文点システムを採用している場合は、取り寄せ注文や予約が多い商品に注目します。あるいは、最終顧客の消費または「プル」に焦点を当てます。逆に需要が激減した場合も同様で、システムやプランナーが過剰に対応することがないようにすべきです。
販売時点予測
バッチサイズ別にグループ化された需要ではなく実際の消費量に基づいて予測・補充モデルを構築することで、真の需要をより明確に把握できます。また、リードタイムや大きなバッチサイズを原因とするスキューを防ぐこともできます。それを実行するためのデータとシステムがある場合は、サプライチェーンの各レベルにおける消費データを調べてみましょう。
予測の集約
もう一つの方法は、プランナーの調整を考慮して、ダウンストリームの調整をアップストリームに伝播させて、ダウンストリームの予測を集約することです。ただ、人間は過剰反応する傾向があり、実際の消費量が隠れてしまう可能性があるので注意が必要です。
マルチエシェロン在庫最適化(MEIO)
最良の在庫最適化を実現するには、多数のレベルに及んでおり内部依存性が考慮されている完全統合アプローチが必要です。この戦略は、在庫を顧客の近くに移動させることでサプライチェーンの在庫を30%削減できる可能性がありますが、一方で、導入時にはサプライチェーン内で鞭効果が発生する可能性があります。まだMEIOを導入していない場合は、需要と供給のバランスが通常のレベルに戻るまで待った方が、システムに新たな衝撃波を与えずに済むかもしれません。
世界と主要産業が新たな正常状態に適応していく中で、製造業者は来る多忙な一年に備えなければなりません。落ち着いて、実際の消費量に注目し、サプライヤーとのコミュニケーションを大切にしてください。それが、顧客からの即時の需要に応え、長期的なレジリエンスを構築する鍵となります。
ステファン・シアンダー(Staffan Theander)は、Syncron Inventoryのプロダクトマネージャーです。シンクロンは、世界中の主要製造業者が世界の新しいサービス経済を活用できるよう支援します。
この記事はSupply & Demand Chain Executive Magazineに掲載されたものです。